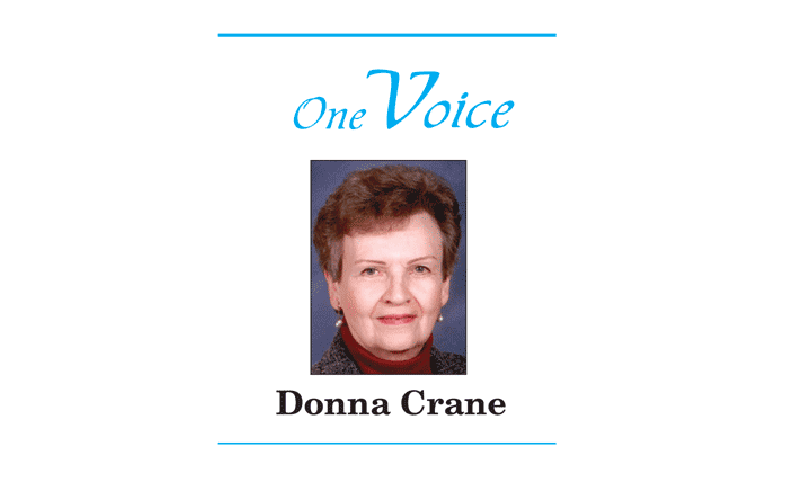
Last of three parts
Adele Peterson has submitted the following article regarding recycling. Parts one and two focused on renovations and sorting of recycling. This week is the series conclusion
“Processing: After materials are sorted, they travel to a reprocessor—such as a paper mill or a plastic reclaimer—to be turned into new materials that can be sent to manufacturers. Inside a facility that reclaims plastic, magnets and other technologies pull any leftover metal out of the trash, and huge grinders chew up plastic into tiny flakes, which can be melted, filtered, and made into plastic pellets that can be shipped to a factory to be remade into something new.
“For some materials, processing works smoothly. Aluminum cans, for example, go to a processing plant that shreds them into tiny pieces, sorts out any stray pieces of plastic or paper, and melts the metal in giant furnaces, to create a valuable material that can be fully reused in new cans. Traditionally, the process hasn’t worked that well for other materials; when you chop up and melt some plastics, the result is a lower-quality material that only can be reused a limited number of times. Other products are hard to recycle because they contain multiple types of plastic, or because the plastic is dyed. But this stage of the recycling process is poised to transform.
“IBM has new technology that can recycle mixed, contaminated, plastic that would have been difficult or impossible to reclaim in the past. A cotton-polyester-blend T-shirt, for example, can be transformed back into pure cotton and pure, virgin-quality polyester. A start-up called Loop Industries has a pilot plant that can use chemical recycling to transform low-value plastic, even ocean plastic, into new, clean packaging for customers such as PepsiCo. A new recycling plant under construction in Ohio will use a gas solvent and filtration to recycle polypropylene, or #5 plastic—something that typically isn’t recycled now, especially when it’s in something like a carpet backing—into a pure new material that can be used to make new food packaging. A biotech company in France recently demonstrated that it could use a biological process to recycle polyester T-shirts or colored plastic bottles into clear bottles.
“Biocellection, another start-up, has a chemical recycling process that can turn polyethylene film—anything from plastic bags to bubble wrap to shrink wrap—into higher-value chemical intermediates that can be made into other products, from nylon to paint. Although the number of places with plastic bag bans are expanding in the U.S., bags are still a key product to figure out how recycle: Some states are trying to stop local governments from enacting the bans, and the EPA estimates that Americans use 380 billion plastic bags and wraps each year. Bags can be recycled into a few products now (though they can’t go through standard sorting equipment, where they can clog machinery), but conventional recycling processes don’t work on them. ‘When you mechanically recycle polyethylene, the end product is not very valuable’, said Jeanny Yao, the co-founder and chief technology officer of Biocellection. ‘So that’s why this type of material is often a big part of what goes into landfill plastic. What we’re trying to do is really make recycling economical by increasing the value of the output of the final thing that you get out of the process.’
‘“To shift the needle and get recycling rates over 10%, you really need to focus on these low-value plastics,’ said Priyanka Bakaya, CEO of a start-up called Renewlogy. The company, which was founded at MIT, works with mixed plastics that otherwise likely wouldn’t be recycled and turns them into a low-carbon, cost-competitive fuel. It currently has a pilot plant in Salt Lake City, another under construction in Canada, and a third in the pipeline in Phoenix.
“Each of these companies is in the early stages, along with others in the space, but their technology could make it more likely that products are recycled. ‘The caveat is that they remain a largely unproven technology,’ said Opsomer. Implemented the wrong way, some argue that some of these new technologies could promote the use of plastics that we might otherwise phase out. ‘It’s saying, hey, your disposable fork, that plastic pouch you couldn’t recycle—all these nonrecyclable plastics, throw them in a bag and, and we’ll somehow do something with it,’ said Bailey. ‘The problem is it’s just perpetuating the cycle of disposable, single-use plastics.’ Still, Yao said, even if we largely eliminate products like plastic straws or forks, we’ll still have a legitimate need for things like plastics used to keep food fresh so it doesn’t end up as food waste—and for those plastics that can’t be recycled easily now, we could soon have better options.
“Paper ends up in recycling bins in huge quantities, including the growing pile of cardboard packages from Amazon and other e-commerce companies. As with plastic, China used to accept mixed paper from the U.S. and then stopped taking it because the loads were so contaminated. But there’s still demand for recycled paper, and that means that paper mills are under construction or reopening in the U.S. ‘What we’re finding is that a lot of companies in China actually still want this material, and since the government isn’t allowing it to come through directly, companies from China are investing in paper mills in the United States,’ said Bridget Croke VP of external affairs at Closed Loop Partners, an investment firm. A company called Nine Dragons Paper bought mills in West Virginia, Wisconsin, and Maine; Shanying International bought a mill in Kentucky. The bales of paper sent to those facilities may be cleaner than what was sent to China in the past. ‘I think the [Chinese ban] has been a strong wake-up call that markets are fragile and we need to clean up our streams and invest in modern equipment to succeed long term,’ she said. That is what is going to improve our material,” Peterson wrote.
Adele Peters is a staff writer at Fast Company who focuses on solutions to some of the world’s largest problems, from climate change to homelessness.